The material used for manufacturing pipe fitting molds varies depending on the specific requirements of the mold, the type of plastic or metal being molded, and the operational conditions the mold will face. Common materials used for making these molds include steel, aluminum, and alloy steel, each of which brings its unique advantages to the table.
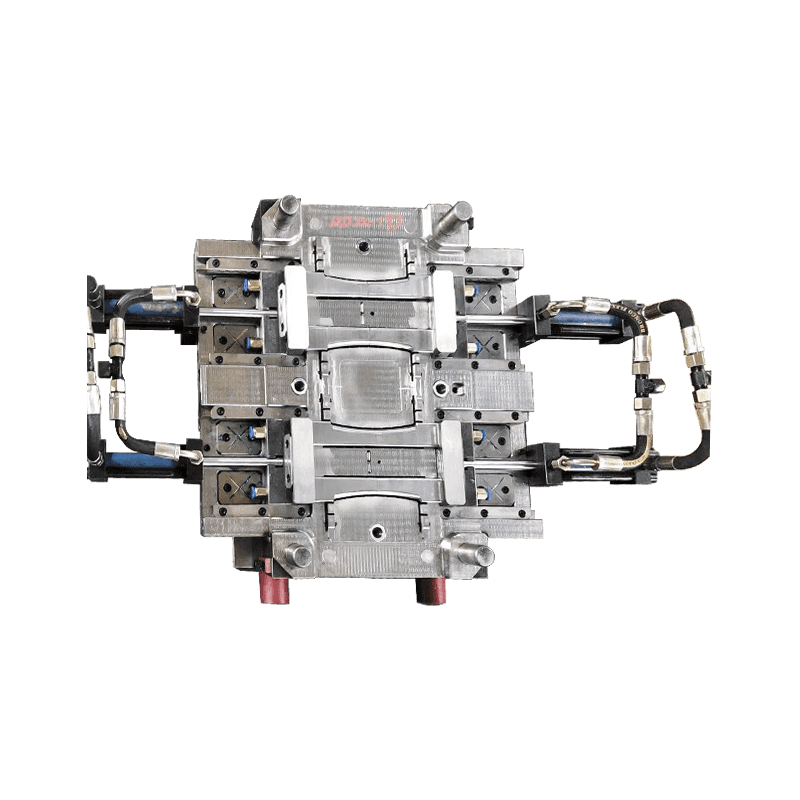
1. Steel (Tool Steel)
Steel is the commonly used material for pipe fitting molds due to its durability and resistance to wear. Steel molds are favored for their ability to produce high volumes of pipe fittings with consistent quality over an extended period. Tool steel, which is specifically designed for high-performance applications, is widely used in manufacturing these molds.
Advantages:
Durability: Steel molds can withstand the stresses of repeated molding cycles and are resistant to wear, making them ideal for mass production.
Heat Resistance: Steel is able to handle the high temperatures involved in the injection molding or casting process, which is crucial when molding materials like PVC, HDPE, or metal alloys.
Precision: Steel molds offer high precision, ensuring that pipe fittings meet the tight tolerances required for proper function and installation.
Disadvantages:
Cost: Steel molds are relatively expensive due to the high cost of materials and the complex manufacturing process required.
Weight: Steel molds are heavy, which can increase handling and shipping costs, particularly for large molds.
Applications: Steel molds are ideal for mass production of pipe fittings made from plastic or metal. They are commonly used in the production of fittings for both residential and industrial plumbing systems, such as elbows, tees, and couplings.
2. Aluminum
Aluminum is another popular material used in the creation of pipe fitting molds, especially for smaller production runs or when faster turnaround times are needed. Aluminum molds are lighter, easier to machine, and less expensive than steel molds, making them a good option for cost-sensitive applications.
Advantages:
Cost-Effective: Aluminum molds are more affordable compared to steel, making them an attractive option for businesses looking to reduce manufacturing costs.
Lightweight: The lighter weight of aluminum molds makes them easier to handle and reduces transportation costs.
Thermal Conductivity: Aluminum has better thermal conductivity than steel, allowing for faster cooling times and higher production efficiency.
Ease of Machining: Aluminum is easier to machine and can be shaped with greater precision compared to steel, which is beneficial for creating intricate mold designs.
Disadvantages:
Lower Durability: While aluminum molds are more affordable, they are less durable than steel molds, which can wear down faster when subjected to prolonged use.
Not Suitable for High-Pressure Molding: Aluminum molds are not as robust as steel molds, which makes them less ideal for high-pressure applications where durability is required.
Applications: Aluminum molds are typically used for producing pipe fittings in smaller batches or for molds that don't need to withstand high pressures or temperatures. They are common in industries that require lower-volume production, such as the production of custom fittings or prototypes.
3. Alloy Steel
Alloy steel is a combination of steel and other elements such as chromium, molybdenum, and vanadium, designed to enhance specific properties like strength, toughness, and resistance to corrosion and wear. Alloy steel molds offer a middle ground between the durability of tool steel and the cost-effectiveness of aluminum.
Advantages:
Strength and Toughness: Alloy steel molds have strength compared to regular steel molds, making them suitable for high-pressure molding processes.
Corrosion Resistance: Alloy steels are often more resistant to corrosion, which is particularly useful when molding materials that are prone to sticking or reacting with mold surfaces.
High Durability: Alloy steel molds offer better longevity than aluminum molds, making them suitable for longer production runs and higher-volume manufacturing.
Disadvantages:
Cost: While alloy steel is generally more affordable than high-end tool steel, it is still more expensive than aluminum molds.
Machining Complexity: Alloy steel molds can be more difficult to machine compared to aluminum, which may increase production time and costs.
Applications: Alloy steel molds are commonly used in industries where medium to high volumes of pipe fittings need to be produced, especially when durability, strength, and wear resistance are key considerations. They are suitable for producing fittings for heavy-duty plumbing, industrial piping systems, and chemical handling systems.
Contact Us