The roots of plastic injection molding trace back to the early 19th century, with the invention of the plastic material. In 1907, Belgian chemist Leo Baekeland created Bakelite, the synthetic plastic, which was a game-changer for manufacturing. Bakelite, a thermosetting plastic, was initially used for electrical insulators and consumer goods. However, it was not until the 1940s that the true plastic injection molding machine was developed.
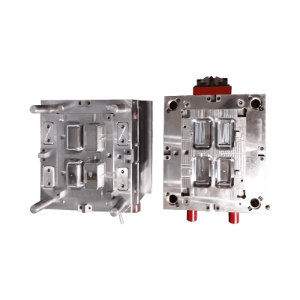
The earliest plastic injection machines were relatively simple devices compared to the technology we have today. They were designed to inject melted plastic into a mold cavity under pressure, where it would then cool and solidify into a final product. This process allowed manufacturers to create complex shapes with great precision and in high volumes, something that was previously impossible with traditional methods like die-casting or stamping.
The injection molding machine, known as the "injection screw machine," was developed by James Watson Hendry in 1946. Hendry's invention laid the foundation for the modern plastic injection molding process, using a screw to feed plastic into the mold, which revolutionized the way plastic components were produced.
As the plastic injection molding process gained popularity, so too did advancements in the materials and technologies used. In the 1950s and 1960s, new types of plastic materials such as polyethylene (PE), polypropylene (PP), and polystyrene (PS) became widely available. These materials were more versatile, cost-effective, and durable than earlier plastics like Bakelite, making them ideal for injection molding.
During this period, the machinery used in the process also evolved. Hydraulic-powered injection molding machines were introduced, providing greater control and precision. These machines allowed for more consistent quality, faster production times, and the ability to create more intricate designs. Additionally, automation began to play a role in plastic injection molding, further improving efficiency.
In the 1980s, the introduction of microprocessor-controlled machines marked a significant leap forward in the injection molding process. These machines featured advanced controls, enabling operators to monitor and adjust various parameters like temperature, pressure, and injection speed, resulting in higher accuracy and reduced production defects.
One of the significant developments in plastic injection molding came with the introduction of multi-cavity molds in the 1990s. Multi-cavity molds allowed manufacturers to produce multiple parts in a single cycle, greatly increasing production efficiency and lowering per-unit costs. This development was particularly beneficial for high-volume production runs, where time and cost efficiency are critical.
Around the same time, multi-material injection molding, also known as overmolding, emerged as a technique that allowed manufacturers to combine two or more materials in a single molded part. This technique is widely used in industries such as automotive, consumer electronics, and medical devices, where combining materials with different properties is essential. For example, a soft rubber grip can be overmolded onto a hard plastic base to create a comfortable, ergonomic handle.
The 21st century has seen remarkable advancements in plastic injection molding technology. One of the notable innovations is the integration of 3D printing into the process. While 3D printing itself is not new, its integration with traditional plastic injection molding has revolutionized prototyping and mold-making. Designers can now use 3D printing to rapidly create prototypes of plastic parts, test their designs, and make adjustments before creating expensive metal molds. This not only speeds up the product development cycle but also reduces costs.
In addition, the adoption of Industry 4.0 technologies has significantly impacted plastic injection molding. Smart factories that employ Internet of Things (IoT) devices, sensors, and machine learning algorithms are now able to monitor production processes in real-time. These systems allow for predictive maintenance, reducing downtime and improving the overall efficiency of the injection molding process. Data analytics also enables manufacturers to optimize production settings, ensuring consistent product quality while reducing material waste.
Contact Us