Injection molding is one of the widely used types of plastic molding due to its versatility and efficiency. In this process, plastic material is heated until it becomes molten and then injected into a mold cavity under high pressure. The material fills the cavity and is cooled to form a solid part. Injection molding is suitable for high-volume production and is used to create parts with complex geometries and fine details.
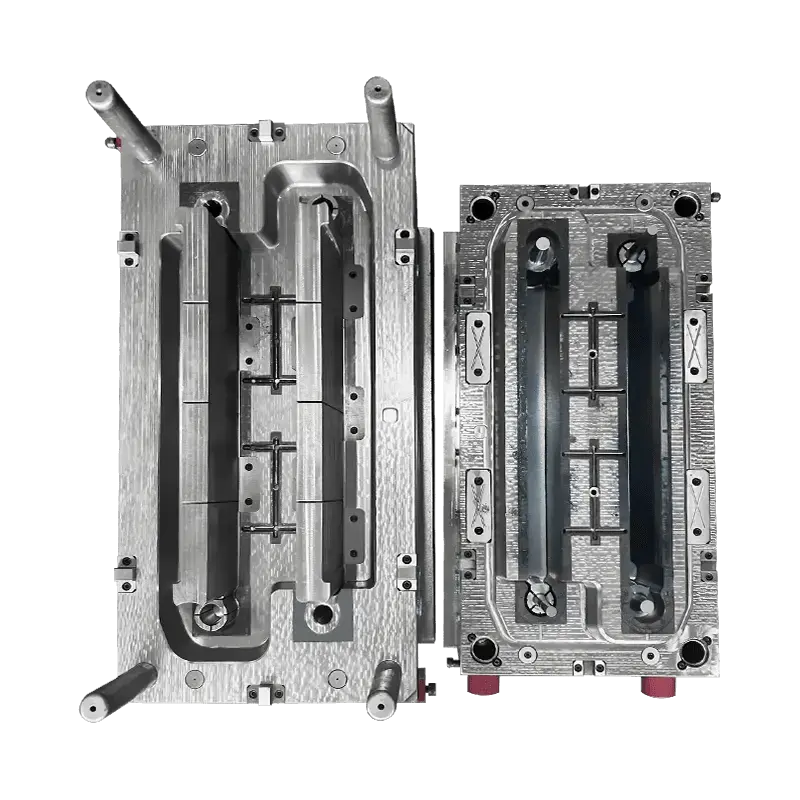
Advantages:
High Efficiency: It's capable of producing large quantities of plastic parts in a short amount of time.
Precision: Injection molds can create parts with high precision, allowing for intricate designs and tight tolerances.
Variety of Materials: Almost any thermoplastic material can be used, including ABS, polystyrene, polypropylene, and polyethylene.
Applications:
Commonly used in industries such as automotive, consumer electronics, medical devices, and packaging.
Blow molding is a specialized form of molding used primarily to create hollow plastic products, such as bottles, containers, and other items with a consistent internal volume. In this process, plastic is heated and formed into a tube-like shape called a parison. The parison is then inflated inside a mold cavity using compressed air, forming a hollow shape.
Advantages:
Cost-Effective for Hollow Products: Blow molding is highly efficient for producing large quantities of hollow plastic items.
Low Material Waste: The process ensures minimal waste of plastic material.
Variety of Shapes and Sizes: Blow molding can produce large items with thin walls, as well as smaller, more intricate designs.
Applications:
Blow molding is used in industries that require plastic bottles, containers, and large hollow parts, such as beverage packaging, personal care products, and automotive industries.
Compression molding involves placing a pre-measured amount of plastic material into an open mold cavity. The mold is then closed, and heat and pressure are applied to the material to force it to take the shape of the mold. Compression molding is typically used for thermoset plastics, which undergo a chemical reaction when heated and cannot be re-melted.
Advantages:
Suitable for High-Volume Production: Compression molding is effective for mass-producing large parts, especially for industries that need durable components.
Cost-Effective: It is generally more affordable than injection molding, especially for large, relatively simple parts.
Strong, Durable Parts: The pressure applied during molding creates robust, strong plastic parts.
Applications:
Commonly used in the automotive, electrical, and appliance industries for manufacturing components like dashboards, electrical housings, and enclosures.
Rotational molding, or rotomolding, is used to create large, hollow plastic products. In this process, plastic powder is loaded into a mold, which is then heated and rotated along two axes. The rotation ensures that the plastic melts and evenly coats the inside of the mold. Once cooled, the mold is removed, and the part is ejected.
Advantages:
Large, Hollow Parts: Rotomolding is ideal for producing large, hollow parts with uniform wall thickness.
Low Tooling Costs: Compared to other molding processes, rotational molding requires relatively low tooling investment.
Design Flexibility: The process can accommodate a wide range of part sizes and shapes.
Applications:
Rotational molding is often used for creating large containers, tanks, playground equipment, and automotive parts.
Thermoforming involves heating a plastic sheet until it becomes pliable, then placing it over a mold and applying pressure to form the shape. The plastic sheet is either vacuum-formed over the mold or press-formed using a mechanical press. This process is ideal for producing relatively simple plastic shapes and products with shallow depths.
Advantages:
Cost-Effective for Low-Volume Production: Thermoforming is more affordable than injection molding for small to medium-sized production runs.
Quick Turnaround Time: The process is faster compared to more complex molding methods.
Simplicity: It's well-suited for producing simpler parts with less intricate details.
Applications:
Thermoforming is used to manufacture packaging materials, trays, and larger consumer goods such as plastic containers, automotive parts, and disposable products.
Contact Us