What Determines the Price of a Plastic Toy Mold?
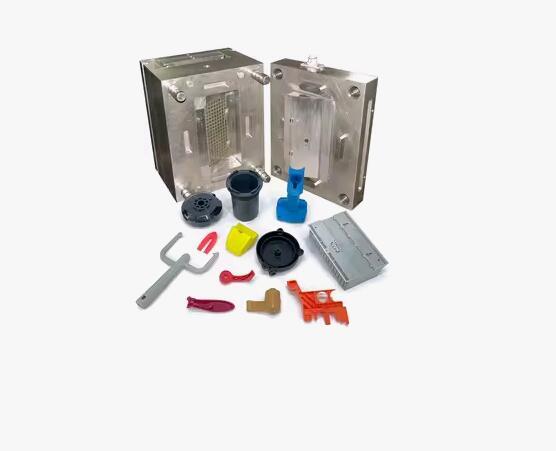
Plastic Toy Mold
The price of a plastic toy mold is not fixed and can vary significantly depending on multiple variables. Some of the primary considerations that affect the pricing include:
Complexity of Design: A simple mold used for basic toy shapes will cost much less than a mold needed for a complex, articulated action figure. Intricate detailing, moving parts, and multi-cavity molds add to the design and machining time, thus increasing the cost.
Material of the Mold: High-quality plastic toy molds are typically made from hardened steel for longevity and durability. However, for short production runs or prototype toys, softer metals like aluminum may be used, reducing the initial cost.
Production Volume Requirements: Manufacturers planning large-scale production are more likely to invest in high-quality molds that can withstand thousands of cycles without degrading. These molds cost more upfront but offer better long-term value.
Precision and Tolerance Needs: Some toys require tight tolerances and high precision, especially when dealing with interlocking parts or components that must move smoothly. High precision in mold manufacturing increases costs due to advanced machinery and skilled labor.
Understanding these factors is critical to evaluating the price situation for a plastic toy mold and determining whether a specific mold meets the intended manufacturing objectives.
General Pricing Ranges in the Market
While prices fluctuate depending on the elements described above, general ranges help illustrate current market conditions:
Basic Plastic Toy Molds: For simple shapes and low-run production, a mold might cost between $1,000 and $5,000. These are typically aluminum-based or made for testing and development phases.
Mid-Range Molds: Molds used for moderately complex toys and intended for mid-sized production runs can range from $5,000 to $20,000.
High-End Molds: Industrial-grade plastic toy molds intended for continuous high-volume production can exceed $50,000, particularly if they include multiple cavities, sliding mechanisms, or require high-precision finishes.
This range reflects the diversity of products in the toy market and the different goals of manufacturers—from small business prototypes to mass-market consumer toys.
Impact of Global Economic Trends
Global economic conditions significantly affect the plastic toy mold price situation. For instance:
Raw Material Costs: Steel and aluminum prices fluctuate with market demand and supply chain conditions. In times of scarcity or increased demand, mold materials become more expensive, increasing overall mold prices.
Labor and Manufacturing Costs: Countries with high labor costs often produce more expensive molds. However, outsourcing to countries with lower production costs has become a common practice to control expenses.
Shipping and Import Fees: International mold purchases involve shipping and tariffs, both of which have seen changes due to global trade dynamics. These costs are often included in the final mold price.
Manufacturers must factor these external conditions into their budgeting when ordering a plastic toy mold, as price variability can impact the overall cost-effectiveness of production.
Balancing Cost and Longevity
When evaluating the cost of a plastic toy mold, it is essential to consider its lifespan and return on investment. While cheaper molds might suffice for small batches, they often wear out faster and may require frequent repairs or replacements. High-quality molds, although more expensive initially, tend to have lower long-term operational costs due to their durability and consistent performance.
Manufacturers looking to maintain high product quality and minimize downtime often prefer investing in premium molds. This balance between cost and efficiency shapes the long-term strategy of many toy production companies.
Contact Us