The production of tool boxes has grown significantly in recent years, owing to the increasing demand for durable and practical storage solutions. Tool box molds are at the core of this manufacturing process, playing a vital role in shaping and forming tool boxes of various types, sizes, and designs. These molds are highly specialized, custom-made tools that enable manufacturers to produce large quantities of tool boxes with precision, ensuring uniformity and high-quality standards.
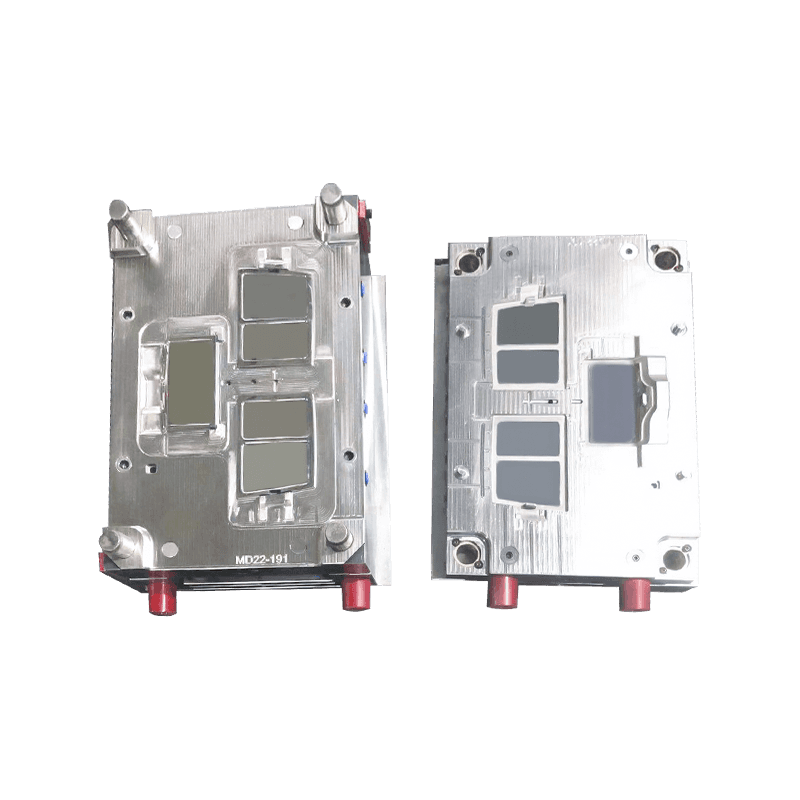
One of the common uses of tool box molds is in the mass production of plastic tool boxes. Plastic tool boxes are widely preferred because of their durability, lightweight design, and resistance to wear and tear. The tool box mold used in plastic injection molding helps shape these boxes into the desired form, which is crucial for ensuring the product is both functional and aesthetically pleasing.
In the plastic injection molding process, the mold is injected with molten plastic material, which then cools and solidifies within the mold cavity. This process is repeated thousands of times, allowing manufacturers to produce large quantities of tool boxes in a relatively short amount of time. The tool box mold must be precisely engineered to accommodate the size and shape of the tool box while maintaining the structural integrity of the product. High-quality molds ensure that the resulting tool boxes are consistent in design, with smooth finishes and well-formed compartments for storing tools.
Customization is another significant use of tool box molds in the manufacturing process. While many tool boxes are standard, off-the-shelf products, there is a growing demand for custom-designed boxes that cater to specific industries or user needs. For instance, tool boxes for automotive repair may require additional compartments or special features, such as reinforced corners for added protection.
By using custom tool box molds, manufacturers can create unique shapes and sizes that meet the specific requirements of their customers. These molds are designed to accommodate features like handle placement, storage dividers, and latch systems. The flexibility of tool box molds enables manufacturers to cater to a broad range of markets, from DIY enthusiasts to professional tradespeople, offering products that are tailored to their needs.
Tool box molds are not only used for production but also play a crucial role in the testing and quality assurance of tool boxes. During the molding process, manufacturers can evaluate the structural integrity of the tool box by testing how well it holds up under stress. For example, the mold may be designed to simulate real-world conditions by applying pressure to specific areas of the tool box or by testing how well it withstands temperatures.
This is essential for ensuring that the final product meets industry standards for durability and performance. Tool box molds are carefully crafted to ensure that the products produced are resilient to damage, even in harsh environments. For industries such as construction, automotive repair, or manufacturing, the durability of the tool box is of importance, and the molding process is integral to ensuring that the final product will stand up to rigorous use.
The use of tool box molds is integral to achieving cost-effectiveness in large-scale production. Manufacturing tool boxes by hand or using traditional methods would be time-consuming and expensive, especially for companies looking to produce hundreds or thousands of units. By utilizing tool box molds, manufacturers can streamline the production process and achieve economies of scale.
Injection molding, for example, allows for the rapid production of tool boxes with minimal labor, reducing overall production costs. This process is highly efficient, producing consistent and uniform tool boxes with little material waste. As a result, companies that rely on tool box molds can keep their costs down while meeting high demand and ensuring that their products are affordable for consumers.
Contact Us