In the world of industrial manufacturing, ensuring the longevity and reliability of equipment is crucial for efficient production and cost management. One critical component that plays a major role in the production of duct exhaust fans is the Duct Exhaust Fan Shell Mold. These molds are used in the creation of the outer casing of exhaust fans, and their durability and service life directly impact the overall efficiency and cost-effectiveness of fan production.
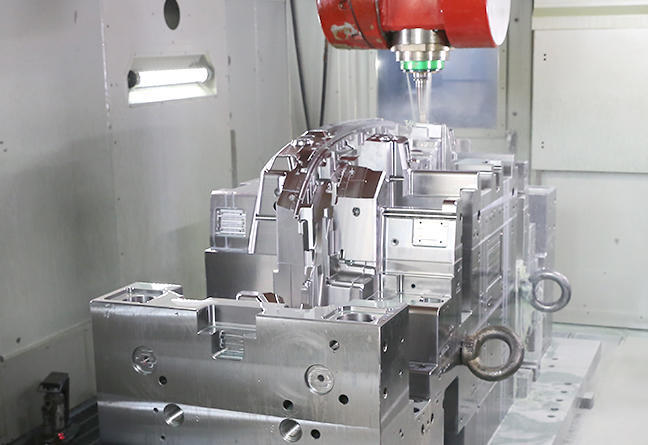
Several factors influence how long a Duct Exhaust Fan Shell Mold will last. These factors include the materials used for the mold, the frequency of use, the quality of the mold's design, and the level of maintenance provided. Understanding these factors can help manufacturers extend the service life of the mold and maintain the high quality of the duct exhaust fans being produced.
The material used in the construction of the Duct Exhaust Fan Shell Mold is one of the important determinants of its service life. Molds made from high-quality steel or aluminum are generally more durable and resistant to wear and tear compared to those made from lower-quality materials. Stainless steel, for example, is known for its resistance to corrosion, rust, and damage from heat, making it an ideal material for molds that will be used frequently.
Over time, even the materials will begin to experience wear, but high-quality materials can significantly extend the life of the Duct Exhaust Fan Shell Mold, making it a worthwhile investment for manufacturers.
The frequency with which the Duct Exhaust Fan Shell Mold is used also plays a major role in determining its service life. Molds that are used for heavy production schedules will experience more wear compared to those used less frequently. High-volume production environments, where thousands of fan casings are molded each day, will naturally cause the mold to degrade more quickly due to the constant heat and pressure applied during the molding process.
However, a Duct Exhaust Fan Shell Mold that is only used for smaller, less frequent runs will last longer due to less intense wear. Manufacturers should balance production needs with the wear-and-tear impact on the mold to optimize its service life.
The design and construction of the Duct Exhaust Fan Shell Mold itself can also affect its durability. Molds that are designed with efficiency and durability in mind are less likely to degrade prematurely. For example, molds with reinforced walls and properly aligned components are less likely to experience physical damage or warping over time.
Additionally, the precision of the mold's construction can affect the quality of the fan casings produced, which in turn impacts the overall efficiency of production. A poorly designed mold may defects in the casing, which could necessitate more frequent repairs or replacements.
Proper maintenance is one of the significant factors in extending the service life of the Duct Exhaust Fan Shell Mold. Regular cleaning, inspection, and lubrication are essential to keep the mold in good working condition. Over time, residue from the molding process can build up on the mold's surface, defects in the fan casings and potential damage to the mold itself. Regular cleaning and maintenance help prevent this buildup, ensuring that the mold continues to perform effectively.
Lubrication is also important to prevent friction and wear on the moving parts of the mold. Without proper lubrication, the mold may become difficult to operate, potential damage and reduced service life. Manufacturers who adhere to a regular maintenance schedule are more likely to get the out of their Duct Exhaust Fan Shell Mold.
Contact Us