Plastic toys are a staple in the global market, combining creativity, safety, and affordability to bring joy to children of all ages. The production of these toys largely depends on the quality and design of plastic molds, which shape and form each piece with precision. Choosing the right plastic toy mold is crucial for manufacturers aiming to produce high-quality toys efficiently and cost-effectively.
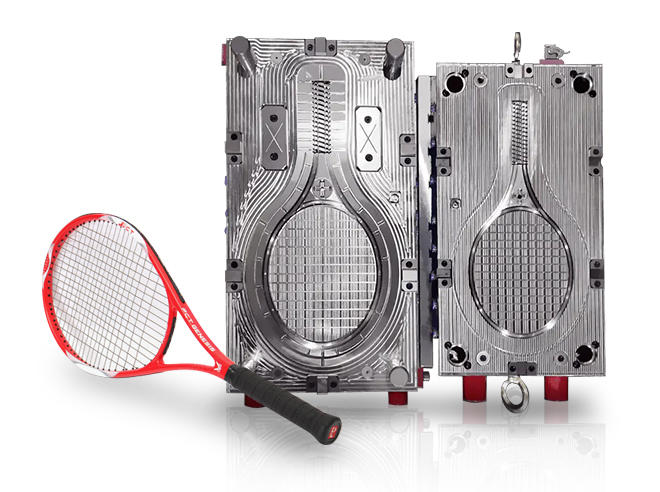
Several critical aspects should guide buyers when selecting plastic toy molds:
1. Material of the Mold
The mold's material affects its durability, precision, and cost. Common materials include:
P20 Steel: A widely used mold steel offering good wear resistance and machinability, suitable for medium production volumes.
H13 Steel: Offers higher heat resistance and toughness, ideal for high-volume production and complex molds.
Stainless Steel: Used for molds requiring corrosion resistance, often in medical or food-safe toy applications.
Choosing the right material depends on production scale, budget, and toy specifications.
2. Mold Design and Complexity
The complexity of the mold reflects the toy's design intricacy. Features such as moving parts, undercuts, and fine details require advanced mold engineering.
Single-Cavity vs. Multi-Cavity: Single-cavity molds produce one toy part per cycle, suitable for prototypes or small batches. Multi-cavity molds yield multiple parts simultaneously, enhancing production efficiency.
Slide and Lifters: Necessary for molds with undercuts or complex shapes, these mechanisms increase mold complexity and cost but are essential for certain toy designs.
A well-designed mold balances complexity with manufacturability and cost.
3. Tolerance and Precision
Toys, especially those with interlocking parts, require tight dimensional tolerances to ensure proper fit and function. High-precision molds reduce post-processing and assembly issues.
Discuss tolerance requirements with the mold maker and verify their capability to meet specifications.
4. Surface Finish
The surface finish of the mold affects the toy's appearance and feel.
Polished Surfaces: Provide smooth, glossy finishes, popular for decorative toys.
Textured Surfaces: Add tactile effects or hide minor imperfections.
Paint Compatibility: Some finishes are better suited for painting or printing.
Specify the desired finish early in the mold design process to avoid costly changes.
5. Cycle Time and Production Efficiency
Efficient mold design can shorten cycle times, increasing output and reducing costs.
Cooling Channels: Well-designed cooling systems promote uniform cooling and faster cycle times.
Ejection Systems: Effective ejection mechanisms ensure smooth removal of parts, defects.
Consult with mold suppliers about these features to optimize production.
6. Safety and Compliance
Toy safety standards vary by region and application. Molds must be designed to produce toys that comply with regulations such as ASTM F963 (USA), EN71 (Europe), and others.
Ensure the mold and final products meet relevant safety requirements, including non-toxic materials and no sharp edges.
Additional Considerations
Mold Maintenance and Longevity: High-quality molds require less frequent maintenance and deliver consistent performance over many cycles. Discuss expected mold lifespan and maintenance needs with the supplier.
Cost vs. Quality Balance: While lower-cost molds may be tempting, they might sacrifice durability or precision, higher long-term costs.
Supplier Reputation: Choose experienced mold makers with proven track records in toy manufacturing.
Prototyping Services: Some suppliers offer prototype molds or rapid tooling to test designs before full production.
The Buying Process: Step-by-Step
Define Product Requirements: Clarify toy design, material, production volume, and finish requirements.
Request Quotes and Proposals: Contact multiple mold makers, providing detailed specifications.
Evaluate Samples and References: Review mold samples and ask for references from previous clients.
Negotiate Terms: Discuss price, time, warranty, and after-sales support.
Design Approval: Work with suppliers to finalize mold design, incorporating feedback and safety standards.
Production and Testing: Upon mold completion, conduct test runs and quality inspections.
Ongoing Support: Establish maintenance schedules and support channels.
Contact Us