One of the main reasons for the wide adoption of ventilation mold is its inherent functionality. Ventilation components are essential in products where air circulation, cooling, or pressure regulation is required. The ventilation mold provides a standardized and efficient way to manufacture these parts consistently.
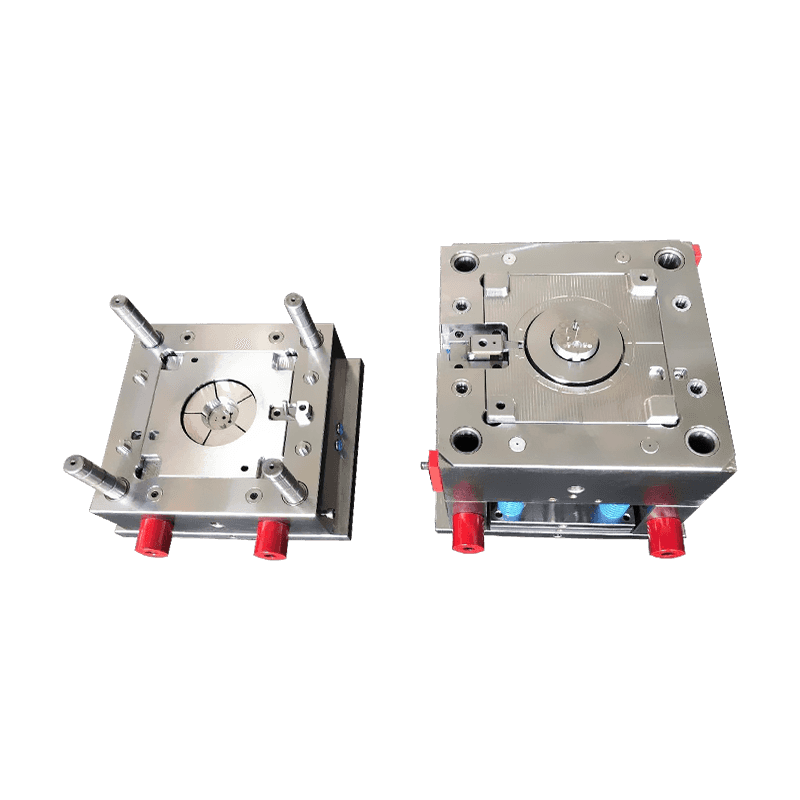
For instance, in automotive interiors, air vents must be precise in shape and size to ensure proper airflow and compatibility with dashboard assemblies. Similarly, in home appliances like air purifiers and refrigerators, vent components produced using a ventilation mold ensure even air distribution and maintain energy efficiency. The mold guarantees that each part fits and performs exactly as needed, which is a significant advantage in high-volume production.
Another factor contributing to the popularity of the ventilation mold is its design flexibility. Manufacturers can customize the mold according to the specifications of the product it will be used for. This flexibility allows engineers to design parts that meet both aesthetic and performance standards without compromising either aspect.
Custom ventilation mold designs allow for integration into products of various shapes, sizes, and surface finishes. Whether a manufacturer requires round, square, slotted, or patterned vents, the mold can be adapted to produce those specifications with consistency. This adaptability ensures that ventilation mold serves a wide range of industries, further increasing its appeal.
In large-scale production, consistency is key. A ventilation mold offers reliable repeatability, ensuring that each vented part meets the same standards as the last. The mold itself is produced using advanced CNC machining and precision techniques, which help ensure accuracy down to the millimeter.
This repeatability is especially valuable in industries where safety and regulatory compliance are important. Products like HVAC ducting or electronic enclosures often need to adhere to strict ventilation requirements. The use of a ventilation mold ensures that all produced components are identical, which reduces variability and the risk of defects.
While the initial cost of creating a ventilation mold can be significant—depending on the material and complexity—the long-term savings it offers are considerable. Once a mold is produced, it can be used thousands of times, significantly reducing the per-unit cost of the final product.
Furthermore, a well-designed ventilation mold minimizes material waste and speeds up the production process, both of which contribute to lower operational costs. For companies looking to scale up production or offer competitively priced products, investing in a high-quality mold becomes a strategic advantage.
Modern ventilation mold designs use robust materials such as hardened steel or aluminum, which allow for high-pressure injection molding and extended use without significant wear. This durability ensures that manufacturers can rely on the mold for long production runs, their investment and reduce downtime due to repairs or replacement.
Moreover, the strength of the materials used in ventilation mold creation allows for complex structures, such as thin vent slats or intricate lattice designs, without sacrificing the integrity of the finished part.
As environmental consciousness increases, many industries are shifting toward sustainable practices. The use of ventilation mold supports this goal in several ways. Molds help reduce material waste by optimizing the molding process. Second, many manufacturers are now using recyclable or biodegradable plastics in conjunction with the molds, contributing to greener production.
Consumers increasingly favor products that demonstrate environmental responsibility. The precision and efficiency provided by a ventilation mold align with this expectation, making it a practical and appealing choice.
Contact Us